Specification
The right size and specification of static compactor will be determined by the size and volume of waste material you are looking to handle and load into the machine. We start with our Simpak 1200 model which is ideal for processing smaller volumes of waste. The Simpak 1500 is physically smaller than the Simpak 1200 but utilises compacting rams set up in a scissor like action. This compactor therefore offers a relatively large charge box in a compact unit, enabling it to process larger volumes of loaded waste when the availability of space is restricted. The Simpak 1800 is our mid to large range compactor suitable for most loading and compacting requirements. The two largest machines in our range (The Simpak 5000 & 7000) are suitable for processing large volumes of waste material – the 7000 is a transfer station type compactor with a full width compacting blade.
The compactors can be manufactured with many hopper variations to accept a variety of manual and mechanical loading requirements. Options include photo electric cells for automatic start, hydraulic clamping, container guides, oil cooler etc.
Power UnitÂ
Hydraulic power is supplied by an integrated, electrically driven power pack built into the rear of the machine (external power packs on top of the rear deck are an option). The force is applied via a double acting hydraulic cylinder *, making full use of the power available. Pressure switches and mechanical overload valves safeguard the system by cutting out when the circuit pressure reaches maximum safe limits.
*The Randalls Simpak 1500 static compactor has two double acting hydraulic cylinders, set up to operate in a scissor like action to reduce space requirements.
Electrical Systems
The main control panel with PLC is situated inside the rear of the machine and incorporates the main isolator. EMERGENCT STOP/start, pre full, full, compactor available and other controls and indicators (if required) are mounted on a separate panel inside a secure box adjacent to the loading area. Power requirements are 415V, 50 HZ on a 3 phase plus earth system.
Safety
All units are manufactured to meet the Health & Safety requirements of the Machinery Directive and other relevant safety standards, including CHEM. Safety switches or fixed guards are located at access points to all reachable moving parts. The hydraulic ram is programmed to retract on starting up to ensure safe operation.
Refurbishment
To maximise the lifespan of compaction units, we can undertake complete refurbishment of damaged or worn out equipment.
Enquire about these products
Model | 1200 | 1500 | 1800 | 1800 Hi-Flow |
5000 | 7000 |
---|---|---|---|---|---|---|
Charge Box Vol cu.m | 1.17 | 1.53 | 1.7 | 1.7 | 3.46 | 5.1 |
Charge Box Loading Aperture Length (mm) | 1010 | 1270 | 1460 | 1460 | 1920 | 2174 |
Charge Box Loading Aperture Width (mm) | 1410 | 1415 | 1420 | 1420 | 1517 | 1952 |
Charge Box Depth (mm) | 825 | 855 | 827 | 827 | 1187 | 1205 |
Packing Blade Height (mm) | 773 | 773 | 773 | 773 | 762 | 713 |
Loading Height (minimum) (mm) | 1250 | 1250 | 1250 | 1250 | 1600 | 2000 |
Throughout M3/HR | 123 | 125 | 128 | 182 | 177.5 | 242.0 |
Compaction Force kgf | 17850 | 19950 | 25650 | 35407 | 45600 | 45600 |
Pinning off Force kgf | 22000 | 22800 | 30000 | 32750 | 51300 | 51300 |
Overall length (mm) | 3230 | 2160 | 4133 | 4133 | 6481 | 7240 |
Overall width (mm) | 1750 | 1772 | 1750 | 1750 | 1740 | 2200 |
Width inc. Load binders (mm) | 2096 | 2122 | 2088 | 2088 | 2114 | 2600 |
Deck height (mm) | 1165 | 1200 | 1165 | 1165 | 1358 | 1685 |
Motor size (kw) | 7.5 | 7.5 | 7.5 | 11 | 22 | 22 |
Cycle time (secs) | 32 | 40 | 45 | 32 | 45 | 45 |
Power supply 415v, 3ph, 50hz, Neutral and Earth | 32A | 32A | 32A | 40A | 63A | 63A |
Blade penetration | 200 | 200 | 220 | 220 | 600 | 600 |
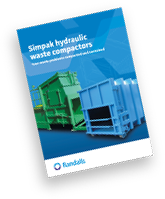